Precision in any field of work is essential. If you want to be on top of your business niche-specific materials and equipment are imperative. Rail linear guidelines are just that, a bearing pillar for many industrial applications. They will guide with barely any friction whilst offering high stiffens for different loads – from a few grams to few pounds. Every performance requirement will easily be met, you just have to choose the right preload, accuracy classification and the actual size of the linear guide. A good place to look at what you need, or just inform on the latest products is tuli-shop.com.
Rail linear guides are the choice for many that require extra rigidity, load profiles and travel accuracy. These types of rails can provide long travelling lengths which makes them superior to other types of guides as well as more accurate. They are also better than simple bearing guides because they have a longer lifespan and are more rigid than guides with bearings.
There are many different rail guides, but ones that stand out in a specific niche are mini rail linear guides. They are compact, up to 3600 mm, and have a small footprint suitable for packaging, food processing, product movement and other similar jobs. They are an economical replacement for standard miniature linear guides that are here for those wanting to save money on maintenance. These are also interchangeable with industry-standard lengths and are made out of aluminium to make sure you get the biggest life span as well as a corrosion-free product.
To keep this type of guides in its fully operating span you have to maintain them properly. Below are tips on just how to do it!
1. Keep the rail surface clean.
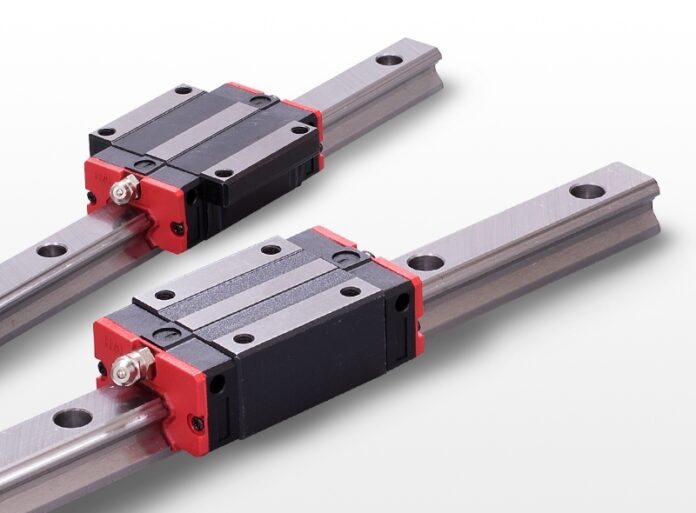
These new mini rail linear guides are really easy to clean and maintain. Since they have ceramically coated and anodized aluminium carriage you don’t have to worry about rust, which is a huge problem with these things. You also have a manufacturer guarantee that it will last a very long time, provided that its installed-on precision mounting surfaces that meet manufacturer tolerances. To maintain its surface, all you have to do is remove any dust or remains from the rail. Depending on its usage or location compressed air is a first thing that will help in blowing off any bigger contaminant. After proceed with alcohol cleaning to remove the smallest specks of dust and dirt. Even though you might not see them with the naked eye they are there and can cause serious damage to the rail. Since these are mini guide rails you will probably need to use cotton picks or balls to clean tighter crevasses to ensure that is impeccable.
2. Rail mounting.
Since these rails are sensitive you should be careful when mounting them, whether it is for the first time or just returning them to their place after maintenance. Aluminium is nice and light, isn’t prone to rust, but it’s also very sensitive to hits and anyone who used it before knows that it easily twists and bends. It is imperative to watch out for hard objects hitting the rail slider and even applying high pressures or overtightening it while mounting.
3. Installation tools.
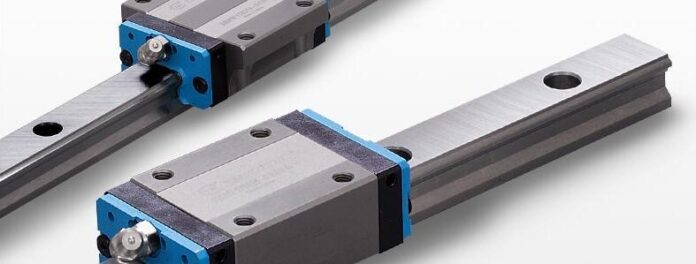
Since these are very precise elements and under very certain guarantees you have to make sure to use appropriate and accurate installation tools. Try and steer clear of short fibre cloths and the likes to keep the mechanism in top shape.
4. Rail Lubrication.
Depending on the type of rail it will either be precoated with some sort of lasting lubricant or you will have to apply some in certain intervals. No matter which, a through step one is crucial. If the surface of the rail isn’t clean enough, applying any sort of lubricant won’t help. On the contrary, it will wear down the surface of the rail and negatively impact it’s load-bearing and precision figures. In industries such as medical precision, mobile home components or printing and electronics, precision and speed is everything meaning that a rough guide rail might move slow, rough and imperfect.
5. Block Lubrication.
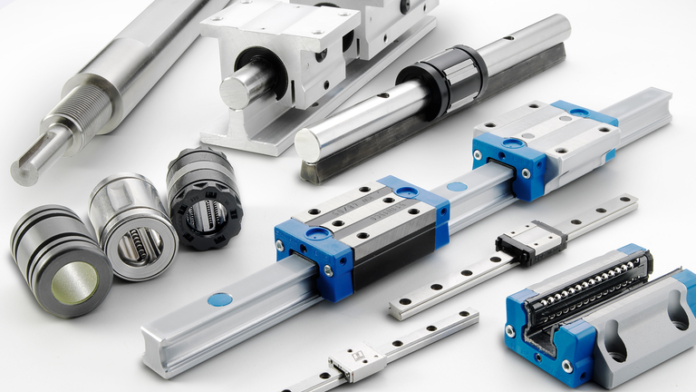
Since the rail is just one part that makes a precise system, you should also consider maintaining the block or the carriage. Depending on the type of rail you will either have a sliding block or rolling one. Both have to be maintained properly, meaning both have to be lubricated properly to do their job. Since sliding blocks have grater friction and need more force to move they have to be checked regularly and lubricated in given intervals. If the block and rail become dry they will produce excessive heat and end up distorting. That means that both of their lifespans will be shorter, but more importantly, accuracy will be lost. Bearing blocks also use lubrication and it is pretty simple to maintain them. If you own a bearing block you will have lubricant fill holes (nipples) on it. Attach the fill hose to the nipple and use an adequate amount of the appropriate lubricant. It should also be noted that excessive amounts will not provide better results. More is not always better which is why you should always consult manufacturers guide on this matter.
The equipment we use in our daily jobs is all about balance. We have to balance the good and the bad to get the best from what we invested in. Proper care, handling and maintenance are often an expense but a necessity if we want to prolong the life of our equipment. Manufacturer guidelines are something easily overlooked but when it comes to products like these, that really shouldn’t happen.
Such a case is here. These mini rail linear guides are very fragile and need a lot of attention. To make sure they stay in service as long as possible try to maintain close to perfect working conditions. That means light loads and regular lubrication of rails and sliders gets you close to so-called permanent service life.